I coulda swore I started a thread here, but I can't find it for the life of me, so here we go...
I run a fabrication and welding shop. We build truck equipment. So on our toolbox line, we run 3 welders on a common gas line that are fed by cylinders at the end. For the past 30 years, it's run with no issue on 1/4" copper line, but crap is starting to fall apart and it's time to upgrade. Had this planned nearly a year ago and then we got slammed balls to the wall with work so we postponed it. We also have porosity issues from time to time that have been narrowed down to either bad mix or not enough volume in the line. Currently going through those issues and I'm sick of fighting it. My plan is to run 3/4" copper soldered tubing with drops at each welder. I've sourced 3/4 to 1/2" npt termination points, and 1/2 npt to CGA580 adaptors for the flow meters on the back of each welder. Currently, running pressure gauges instead of flow meters there. I'm considering switching from single tank at a time operation to 6packs just to lessen changeover time. We blow through about a tank a day.
Any opinions on this setup? Any ideas on the pigtail sizing or where I could get oversized pigtail hoses for linking the 6pack or tank to the 1/2 npt drop for the inlet? I welcome all ideas and criticism, I only want to do this once.
I'll post a couple pics in a minute of the current situation. My concern is there currently isn't enough flow to each welder with the tiny ass tubing and that the 3rd welder on the line gets starved out. Also does anybody have any input or experience with gas saver systems?
www.betterwelds.com
Thanks.
I run a fabrication and welding shop. We build truck equipment. So on our toolbox line, we run 3 welders on a common gas line that are fed by cylinders at the end. For the past 30 years, it's run with no issue on 1/4" copper line, but crap is starting to fall apart and it's time to upgrade. Had this planned nearly a year ago and then we got slammed balls to the wall with work so we postponed it. We also have porosity issues from time to time that have been narrowed down to either bad mix or not enough volume in the line. Currently going through those issues and I'm sick of fighting it. My plan is to run 3/4" copper soldered tubing with drops at each welder. I've sourced 3/4 to 1/2" npt termination points, and 1/2 npt to CGA580 adaptors for the flow meters on the back of each welder. Currently, running pressure gauges instead of flow meters there. I'm considering switching from single tank at a time operation to 6packs just to lessen changeover time. We blow through about a tank a day.
Any opinions on this setup? Any ideas on the pigtail sizing or where I could get oversized pigtail hoses for linking the 6pack or tank to the 1/2 npt drop for the inlet? I welcome all ideas and criticism, I only want to do this once.
I'll post a couple pics in a minute of the current situation. My concern is there currently isn't enough flow to each welder with the tiny ass tubing and that the 3rd welder on the line gets starved out. Also does anybody have any input or experience with gas saver systems?
BetterWelds – Gas Saver System
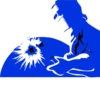
Thanks.