holdmypocket
nil
I've made enough progress to move this into a build thread and I also have some questions/need some sanity-checks at this point so here it is.
I'm starting with a 78 F150 4x4 that I've put a new motor in (400), rebuilt transmission (C6), 2" lift with 33's and overall made into a solid driver. I've been planning this build since 2015 before I even got the truck (I bought it in VA at the end of 2017). A lot of adjustments to that plan and a lot of research/learning but I finally committed this month and got started.
Parts I'm using (I'll update as I go along):
- 2005 Dana 60 out of an F350
- 2014 Sterling 10.5 with e-locker out of an F350
- WFO Radius Arms
- WFO Drag-link kit that uses the stock Ford drag-link end on the axle side with a 1-ton TRE on the pitman arm side
- RuffStuff frame outriggers
- BattleBornBrakes.com coil bucket w/shock mount -These are out boarded enough to use stock super duty coils and the stock axle coil bucket. A super duty coil lifts this set-up the lift height of the coil +1", and the lower bucket mount is higher than the Dana 44 mount by about 1".
- Skyjacker F525V 2.5" Softride Coil for a 2005 F350 4x4 - Take the above into consideration and I'm estimating about 4.5" total lift.
- BroncoAir.com adjustable shackle reversal kit (Shackle Reverse Brackets) - I have Deaver 5.5" lift springs but ran them without the 3.5" factory block. With the adjustable shackle reversal kit and no block I should be able to dial in the rear to be level with the front.
Before Tear Down
I'm starting with a 78 F150 4x4 that I've put a new motor in (400), rebuilt transmission (C6), 2" lift with 33's and overall made into a solid driver. I've been planning this build since 2015 before I even got the truck (I bought it in VA at the end of 2017). A lot of adjustments to that plan and a lot of research/learning but I finally committed this month and got started.
Parts I'm using (I'll update as I go along):
- 2005 Dana 60 out of an F350
- 2014 Sterling 10.5 with e-locker out of an F350
- WFO Radius Arms
- WFO Drag-link kit that uses the stock Ford drag-link end on the axle side with a 1-ton TRE on the pitman arm side
- RuffStuff frame outriggers
- BattleBornBrakes.com coil bucket w/shock mount -These are out boarded enough to use stock super duty coils and the stock axle coil bucket. A super duty coil lifts this set-up the lift height of the coil +1", and the lower bucket mount is higher than the Dana 44 mount by about 1".
- Skyjacker F525V 2.5" Softride Coil for a 2005 F350 4x4 - Take the above into consideration and I'm estimating about 4.5" total lift.
- BroncoAir.com adjustable shackle reversal kit (Shackle Reverse Brackets) - I have Deaver 5.5" lift springs but ran them without the 3.5" factory block. With the adjustable shackle reversal kit and no block I should be able to dial in the rear to be level with the front.
Before Tear Down
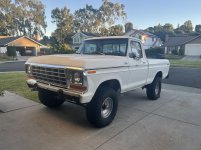